Thread Rolling Process
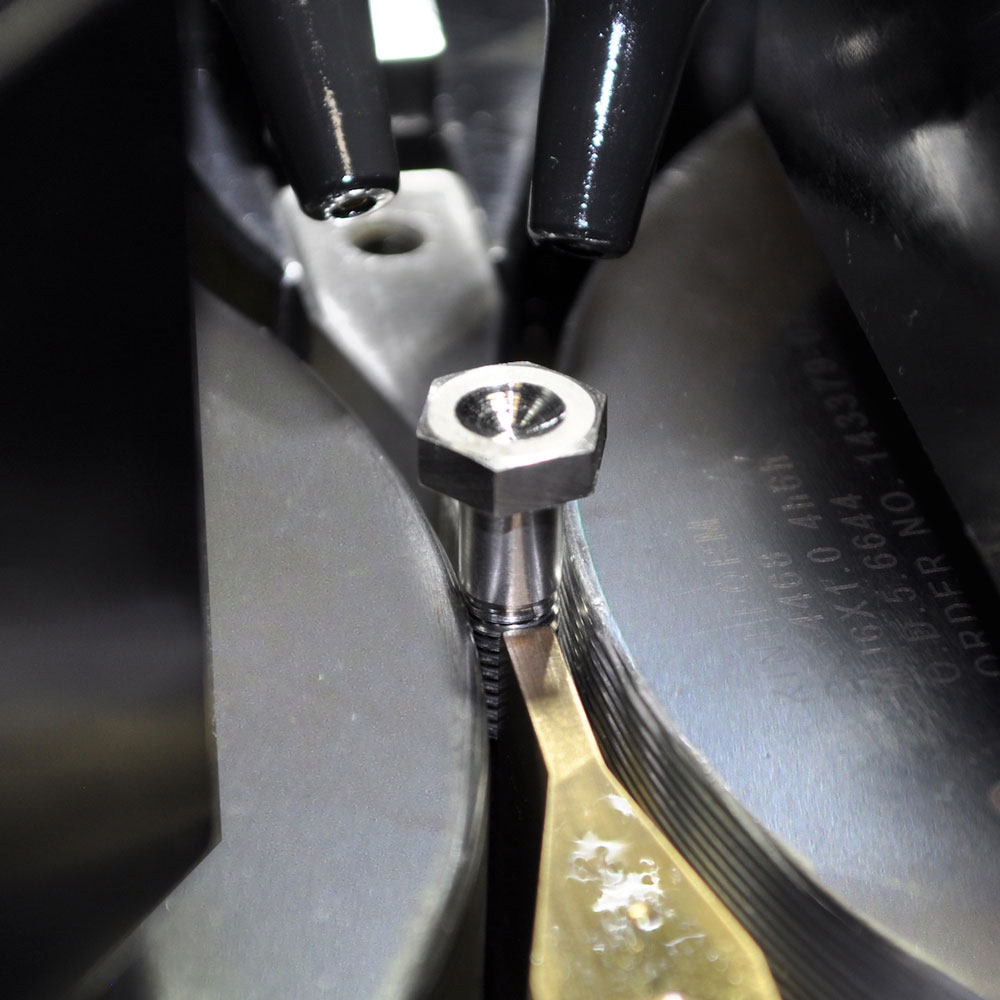
Thread Rolling & Profile Rolling
Through continuous innovation over its 60-year history, Kinefac has led the industry in the development of cylindrical die thread rolling processes. Kinefac thread rolling processes provide significant advantages over thread cutting in strength and fatigue resistance and offer superior surface finish and material savings. Screw threads are used in applications such as fasteners, linear actuators, and fluid connections. Machine screws, bolts, wood screws, bone screws, threaded rod, pipe fittings, and lead screws are the most common types of threaded components produced on Kinefac equipment.
Screw threads are typically rolled using an infeed, throughfeed, or plungefeed rolling process. Kinefac two-die and three-die rolling processes can roll both solid and hollow parts to exact specifications. Precision thread class tolerance levels such as Inch Class 2A and 3A (6g and 4h/6h ISO Metric) are easily achievable by Kinefac controlled thread rolling process.
Benefits of Thread Rolling
|
|
Thread & Profile Geometry
Standard thread forms consist of a profile geometry described by straight side flanks with crest flat, root flat, and radius transitions at fixed pitch spacing. The 60° thread form with 30° flank angles is one of the most common thread profiles and has become a standard for fasteners around the world. The second most popular thread profile is the 29° ACME and Stub-ACME thread form with 14.5° flank angles. Kinefac processes can produce not only these standard forms, but many variations of thread forms ranging from 10° to 30° trapezoidal thread profiles to 5° to 40° buttress thread profiles. Special thread forms like tapered or straight pipe thread profiles, ball screw thread profiles, rope thread profiles, and involute worm gear profiles are also possible. Most threads are rollable using the cylindrical die rolling process.
Kinefac Thread Rolling Process
Key Requirements | Benefits |
---|---|
Stability, rigidity, and control accuracy of the thread rolling machine | Consistent pitch diameter |
Accuracy and precision of the thread rolling dies | Profile and lead quality |
Rotational synchronous accuracy of the thread rolling dies | Maintain die match with the work piece |
Stability of the workpiece throughout the rolling process | Avoid drunken threads and runout |
Size of the pre-roll blank diameter | Achieve correct fill of the thread major diameter |
Sufficient penetration speed of the thread rolling dies into the blank | Avoid over-fatigue and deep seams |
Sufficient dwell time when dies have reached their final penetration position | Roundness calibration |
Minimal friction between the workpiece and work support tooling | High quality thread crest finish and geometry |
Superior Thread Rolling for Demanding Applications
Automotive
Aerospace
Construction
Alternative energy
Fittings
Oil industry
Hardware
Appliance
Advanced Thread Rolling Control Features
POWERBOX machine structure
KINEFORM thread rolling dies
True Die Position system
Auto-Assist Die Matching
Flat blade, roller blade, bushing, and center support tooling
KineGlide low friction rolling blades
Servo blade automatic height control systems
Warm rolling systems
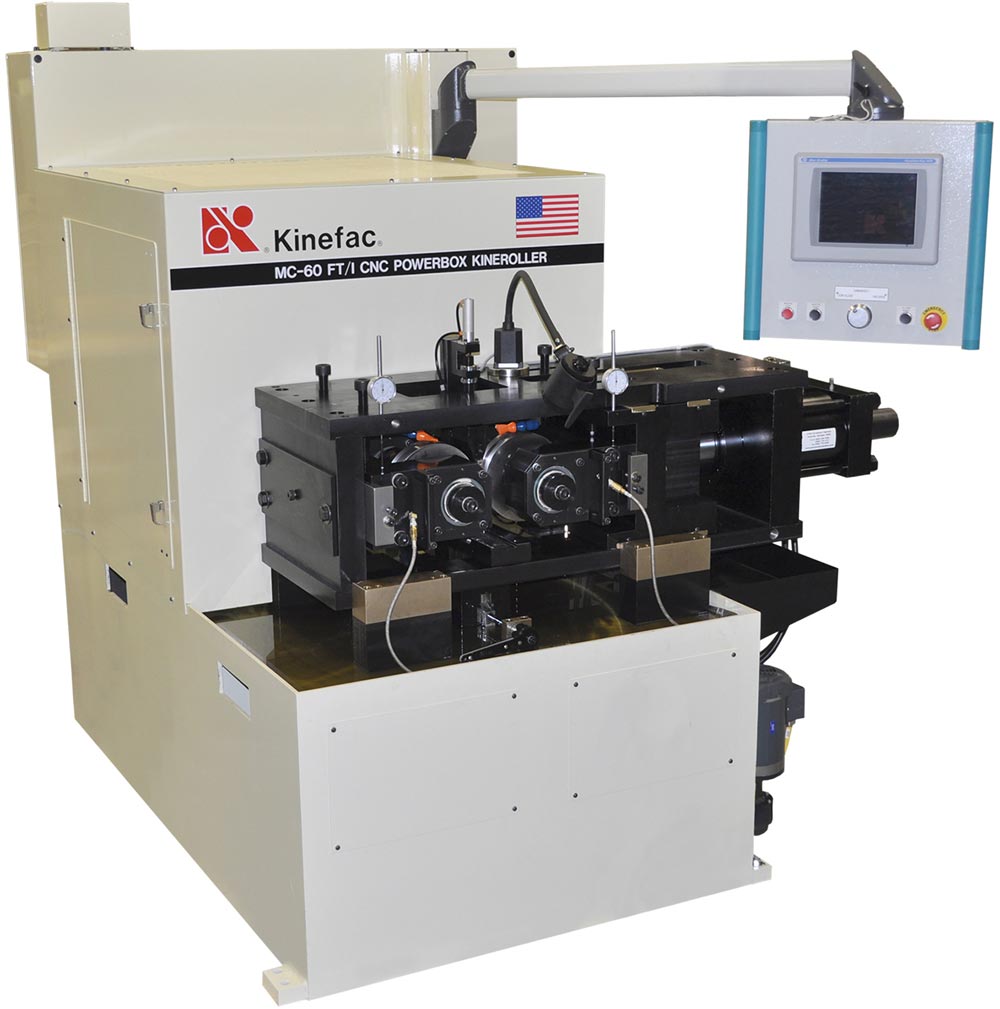
Advanced Thread Rolling Control Features
POWERBOX machine structure
KINEFORM thread rolling dies
True Die Position system
Auto-Assist Die Matching
Flat blade, roller blade, bushing, and center support tooling
KineGlide low friction rolling blades
Servo blade automatic height control systems
Warm rolling systems
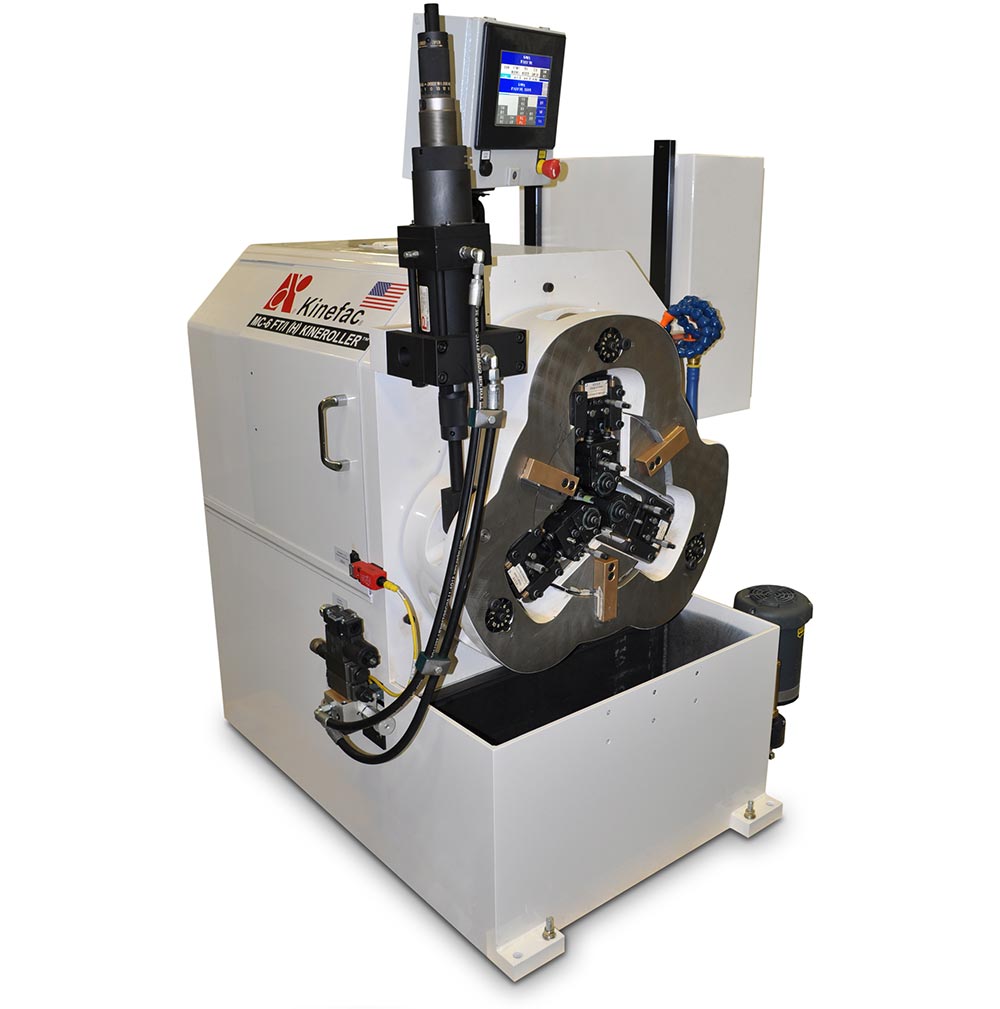