Knurl Rolling Process
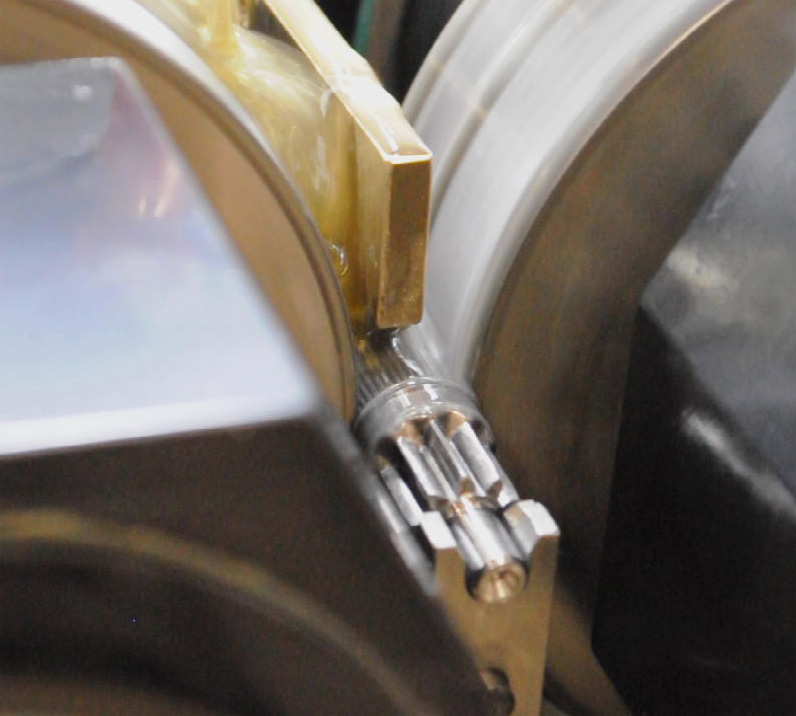
Knurl Rolling
The Kinefac cylindrical die rolling process for knurls responds to the increasing demands for knurl forms used in applications requiring grips, press fits, or over-mold features. Ratchet handles, door pulls, motor armature shafts, and grip nails are common types of knurled components. The Kinefac KineGrip knurl form is a special press fit knurl configuration which increases the concentricity and grip power of the press fit while reducing the press-on forces.
Functionally, knurls differ from splines and serrations in that they typically do not have a precision slip fit with a mating part which requires high-accuracy tooth spacing characteristics. Knurls can be rolled on various components to precision tolerance levels using the Kinefac infeed, single-revolution, or throughfeed rolling processes.
Benefits of Knurl Rolling
|
|
Knurl Geometry
Standard knurl forms consist of a profile geometry described by straight or involute flanks with crest flat, root flat, and radius transitions spaced at a fixed chordal pitch. Knurl forms are either straight (parallel to the axis of the part) or diagonal (at a helix angle up to about 45°). Overlaying left-hand and right-hand forms at equivalent helix angles results in a diamond knurl profile.
Knurls are generally classified by diametral pitch which is the total number of teeth around the circumference divided by the pre-roll blank diameter, or by circular pitch which is the number of teeth per linear inch of circumference. Space angles ranging from 90° to 70° are found on most standard knurls around the world. ASA B94.6 and DIN82 specifications define the industry standard configurations for a variety of course, medium, and fine knurls in 64, 96, 128, and 160 diametral pitches.
Special knurl forms with modified crest flat, root flat, and flank angle geometries serve different functional purposes. The Kinefac KineGrip knurl is an excellent example which uses a comparatively wide root flat and thin crest flat for precision press fit applications. Most knurl forms are rollable using the cylindrical die rolling process.
Kinefac Knurl Rolling Process
Key Requirements | Benefits |
---|---|
Stability, rigidity, and control accuracy of the rolling machine | Precise and repeatable knurl dimensions and good visual appearance |
Accuracy and precision of the knurl rolling dies | Profile quality and good chordal tooth spacing |
Rotational synchronous accuracy of the knurl rolling dies | Maintain die match with the work piece |
Stability of the workpiece throughout the rolling process | Avoid mis-tracking and runout |
Size of the pre-roll blank diameter | Achieve the correct number of teeth, chordal tooth spacing, and required fill of the knurl major diameter |
Sufficient penetration speed of the knurl rolling dies into the blank | Avoid over-fatigue and deep seams |
Sufficient dwell time when dies have reached their final penetration position | Roundness and form calibration |
Minimal friction between the workpiece and work support tooling | Prevent scuffing or other damage to the knurl form during rolling |
Superior Knurl Rolling for Demanding Applications
Door pulls
Weight barbells
Motor armature shafts
Grip nails
Dental tools
Medical device handles
Knurl Rolling Process Control Features
True Die Position system
Flat blade, roller blade, bushing, and center support tooling
Servo blade automatic height control systems
KINEFORM cylindrical rolling dies
KINEGLIDE low friction rolling blades
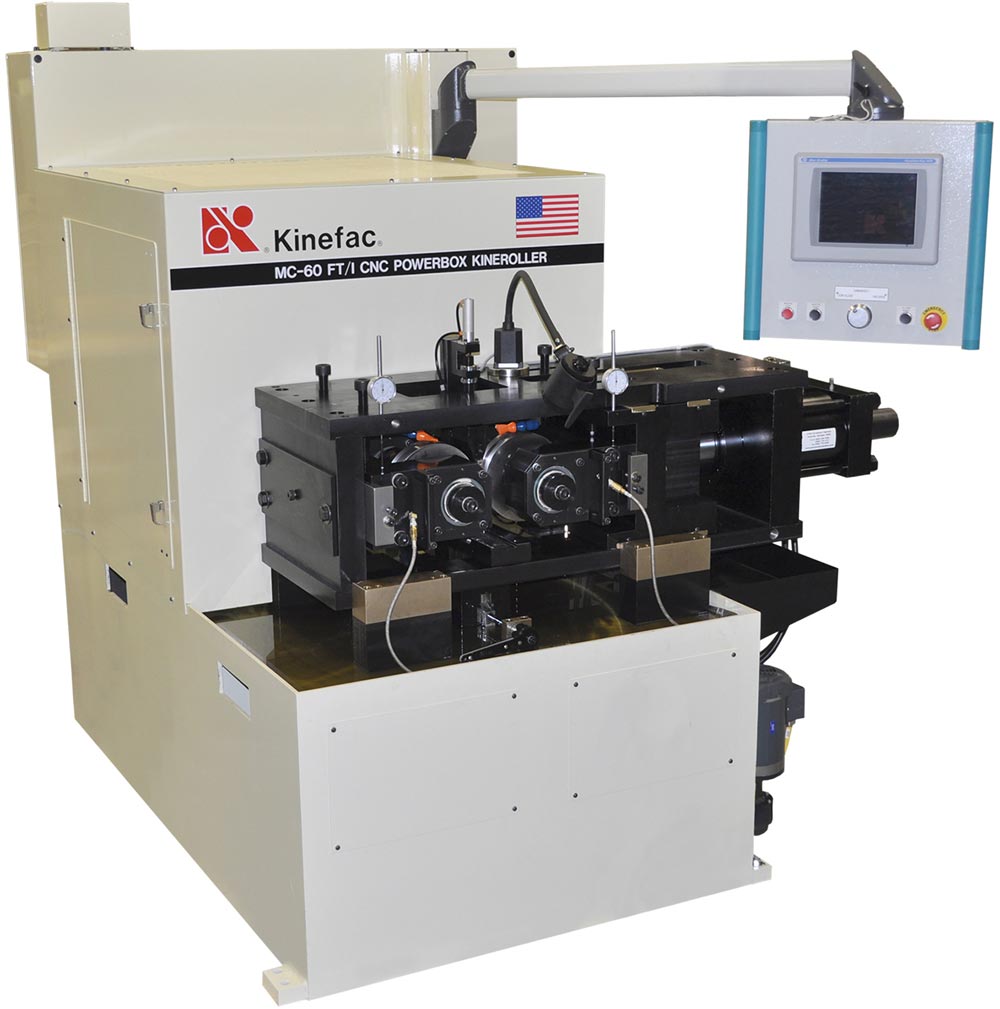
Knurl Rolling Process Control Features
True Die Position system
Flat blade, roller blade, bushing, and center support tooling
Servo blade automatic height control systems
KINEFORM cylindrical rolling dies
KINEGLIDE low friction rolling blades
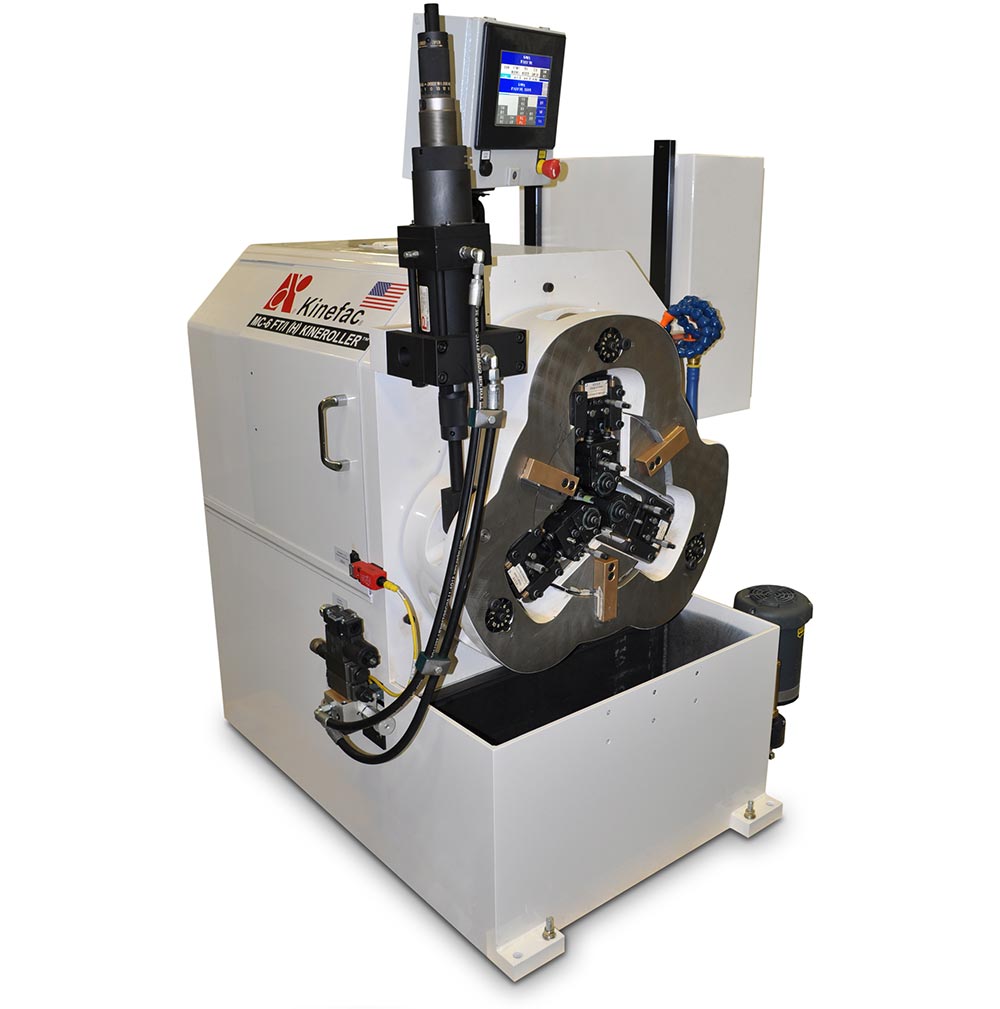