Fin Tube Rolling Process
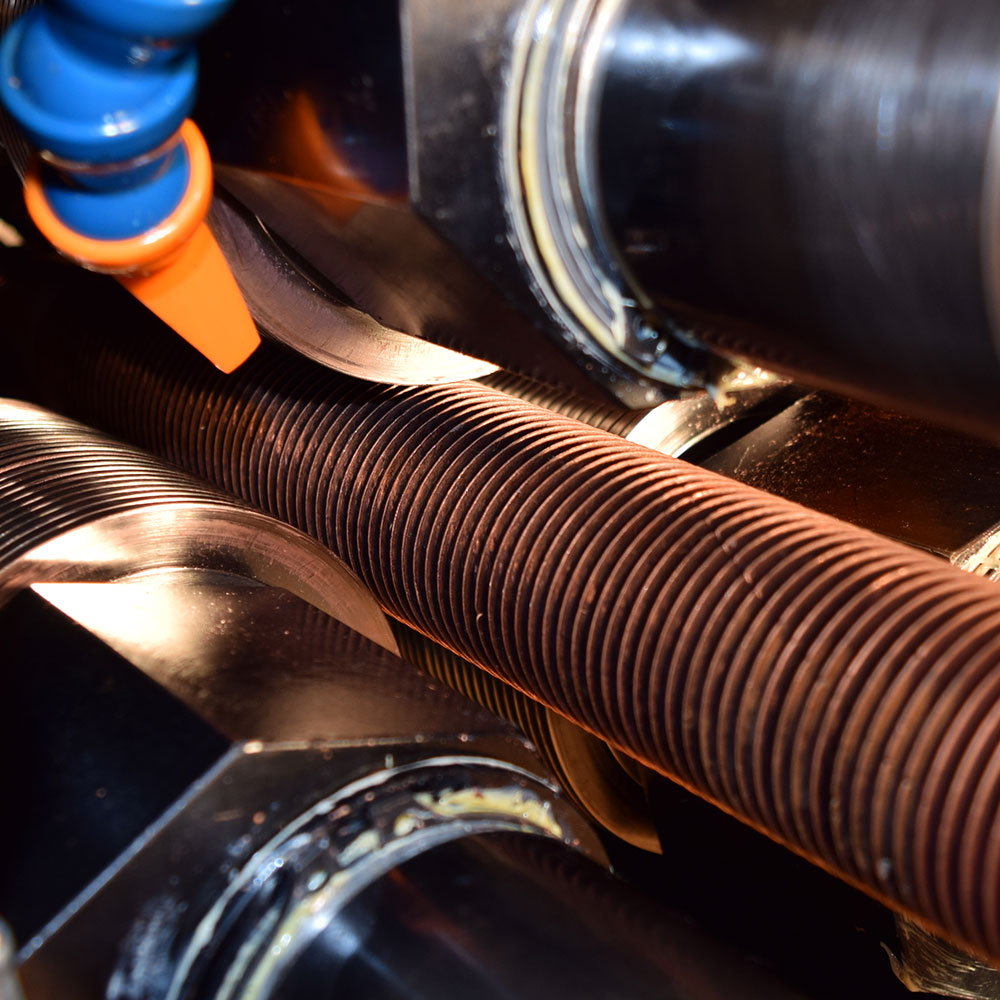
Fin Tube Rolling
Kinefac high-speed fin rolling processes are designed for both low-fin and high-fin heating and cooling applications. Heat exchanger tubes for air conditioners, refrigerators, and heaters are the most common types of finned tube components.
Fins are typically rolled on materials such as copper, aluminum and steel using throughfeed or plungefeed rolling with three dies and an internal mandrel. The internal mandrel supports the tube during rolling and can be profiled to generate finlike forms on the internal surface of the tube to increase surface area and induce turbulence and mixing of working fluids for enhanced heat transfer.
A combination of throughfeed and plungefeed rolling can be used to generate continuous finned sections with blank spacing in between for baffle spacing or where subsequent tube bending operations are carried out.
Benefits of Fin Rolling
|
|
Fin Tube Geometry
Fin tube forms consist of a profile geometry described by straight side flanks with crest flat, root flat, and radius transitions at fixed pitch spacing, as well as a wall thickness under the fins. Fin tube profiles tend to have low flank angles of 10° or less and are typically characterized by the number of fins per inch (FPI) and the height of the fins.
Low fin, medium fin, and high fin classifications range from 5 to 8 FPI up to 50 to 60 FPI. Low fins are generally 1/8” (3mm) or less; medium fins are generally ¼” (6mm) or less; and high fins can be up to ½” (12mm) or more. Fin tubes geometry can also be multi-start.
Most every manufacturer’s fin geometry is unique in some way. The two most common styles of rolled fin tubes are profiles with a diameter-over-fin equal to the pre-roll blank with a significantly reduced inside diameter, and profiles with a diameter-over-fin which is greater than the pre-roll blank and little to no reduction in inside diameter. Fin tube specifications are generally governed by ASME Boiler and Pressure Vessel Codes such as SB359. Most fin profiles can be rolled using the Kinefac three cylindrical die rolling process with consideration of wall thickness, fin height, and fin spacing.
Kinefac Fin Tube Rolling Process
Key Requirements | Benefits |
---|---|
Stability, rigidity, and control accuracy of the rolling machine | Consistent root diameter |
Accuracy and precision of the finning discs (dies) | Profile shape and fin spacing |
Accuracy and precision of the spindle tilt angle adjustment | Fin spacing and number of leads |
Stability of the workpiece throughout the rolling process | Consistent quality and runout |
Size of the pre-roll blank diameter and wall thickness | Achieve correct fin major diameter and wall thickness under fins |
Quality of the pre-roll blank material | Avoid cracking and visual deficiencies |
Sufficient penetration speed of the finning dies into the blank | Generate radial extrusion of the fins |
Sufficient dwell time when dies have reached their final penetration position | Calibrate form roundness |
Properly sized support mandrel | Ensure wall thickness and rolled fin height |
Superior Fin Tube Rolling for Demanding Applications
Refrigeration units
Shell and tube heat exchanger
Air conditioning units
De-Humidifiers
Liquid heating units
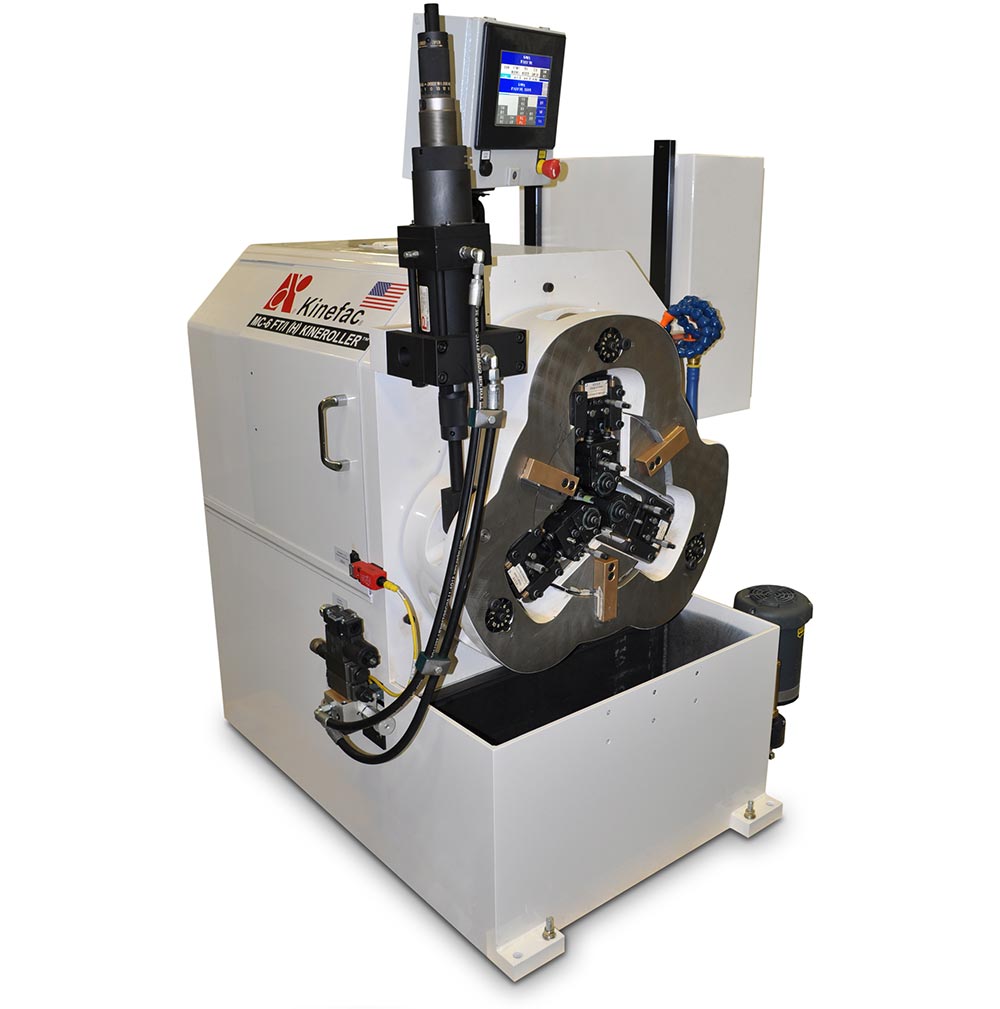
Advanced Fin Tube Rolling Control Features
- Kinefac 3-Die machine structure.
- True Die Position system with electric or hydraulic servo.
- Independent fin disc axial position adjustment with on-screen readout.
- Independent fin disc tilt angle adjustment with on-screen readout.
- KINEFORM fin tube rolling disc dies.
- KineMat input and output automatic and manual tube handling units