Ball Screw Rolling Process
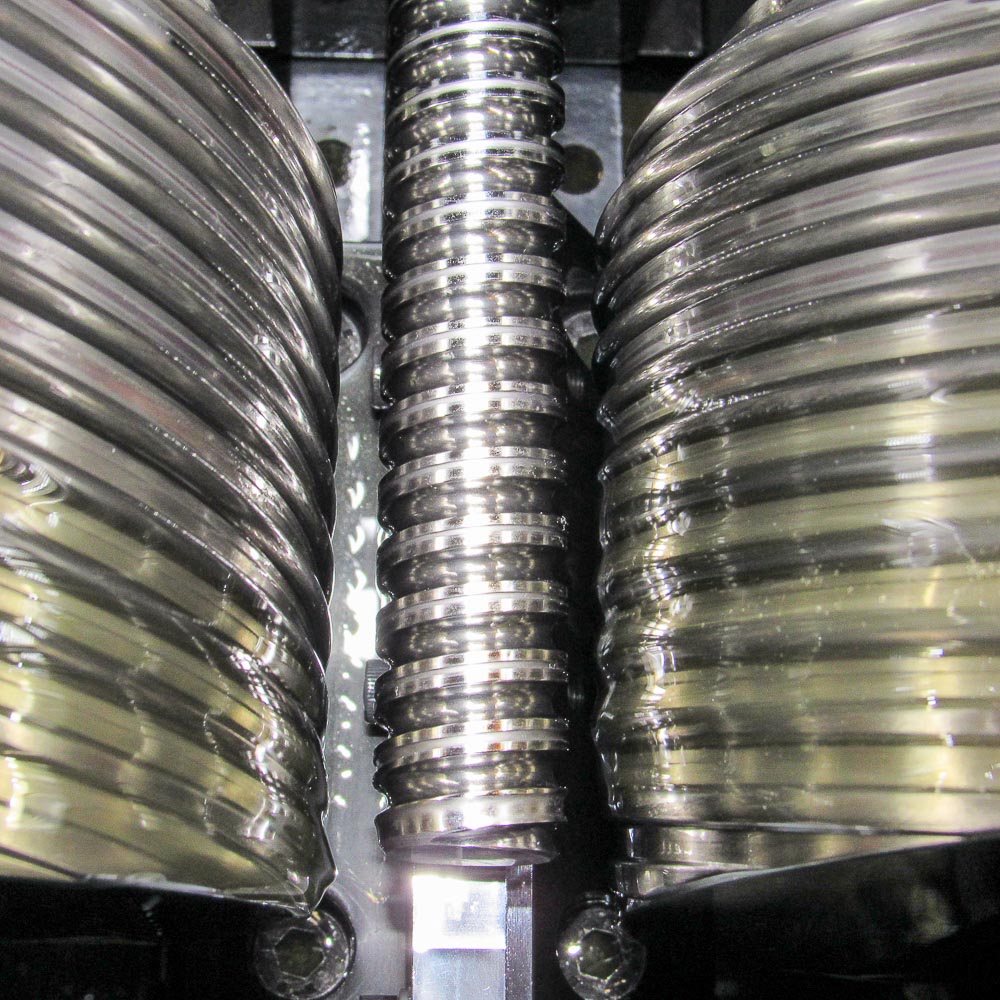
Ball Screw & Lead Screw Rolling
Kinefac high precision ball screw and lead screw rolling equipment offers superior advantages for linear motion control applications requiring high accuracy. Ball screw and lead screw forms are used in linear actuators for transport and positioning purposes. Machine tool slide screws, electric power steering racks, electric window actuator screws, electric seat actuator screws, and electric press actuator screws are common types of ball screw and lead screw components that can be processed on Kinefac equipment using throughfeed, plungefeed, and infeed rolling processes. Kinefac precision ball screw equipment can achieve ball screw lead classes of C10 to C7 or better through its highly controlled rolling process. Kinefac precision lead screw equipment can achieve lead tolerances within 0.002” per foot or better.
Benefits of Ball Screw Rolling
|
|
Ball Screw Geometry
Ball screw forms consist of a profile geometry described by a single full radius or two intersecting offset gothic radii at fixed pitch spacing with blended transitions. The relationship between the size, depth, and spacing of the radii generates the ball screw profile, with the intersecting gothic arc design being the most popular. There are many variations of ball screw forms having narrow or wide crest flats and single or multiple starts. The most important characteristics of a ball screw are the measure-over-wire (or measure-over-pin or measure-over-ball) and lead or pitch spacing of the ball grooves over a specific length.
Lead Screw Geometry
Lead screw forms consist of a profile geometry described by straight flanks with a crest flat, root flat, and radius transitions at fixed pitch spacing. The most popular types of lead screw forms are the ACME and trapezoidal profiles with flank angles ranging from 10° to 30°. These forms can also be single or multi-start. Special lead screws such as 5° to 40° buttress thread profiles are also rollable using the Kinefac cylindrical die rolling process. The most important characteristics of a lead screw are the dimension-over-wire and lead or pitch spacing of the threads over a specific length.
Kinefac Ball Screw Rolling Process
Key Requirements | Benefits |
---|---|
Stability, rigidity, and control accuracy of the thread rolling machine | Consistent measure-over-ball or measure-over-wire diameters |
Accuracy and precision of the thread rolling dies with sufficient form calibration | Profile and lead quality |
Rotational synchronous accuracy of the thread rolling dies | Maintain die match with the work piece |
Controlled thermal stability of the thread rolling dies and workpiece | Maintain precision lead and diametral tolerances |
Stability and alignment of the workpiece throughout the rolling process | Maintain cylindricity of the helix and to avoid drunken thread conditions |
Size of the pre-roll blank diameter | Achieve correct fill of the major diameter and crest seam |
Minimal friction between the workpiece and work support tooling | High quality thread crest finish and geometry |
Superior Ball Screw Rolling for Demanding Applications
Automotive Brake Actuation Shafts
Medical Device Delivery System Shafts
Industrial Equipment Actuation Screws
Aerospace Actuation Screws
Solar Panel Actuation Shafts
Precision Ball Screws
Actuator Screws
Ball Screw Rolling Process Control Features
True Die Position system
Chilled die and part lubrication systems
KINEFORM cylindrical rolling dies
Servo blade automatic height control systems
KineGlide low friction rolling blades
Flat blade, roller blade, bushing, and center support tooling
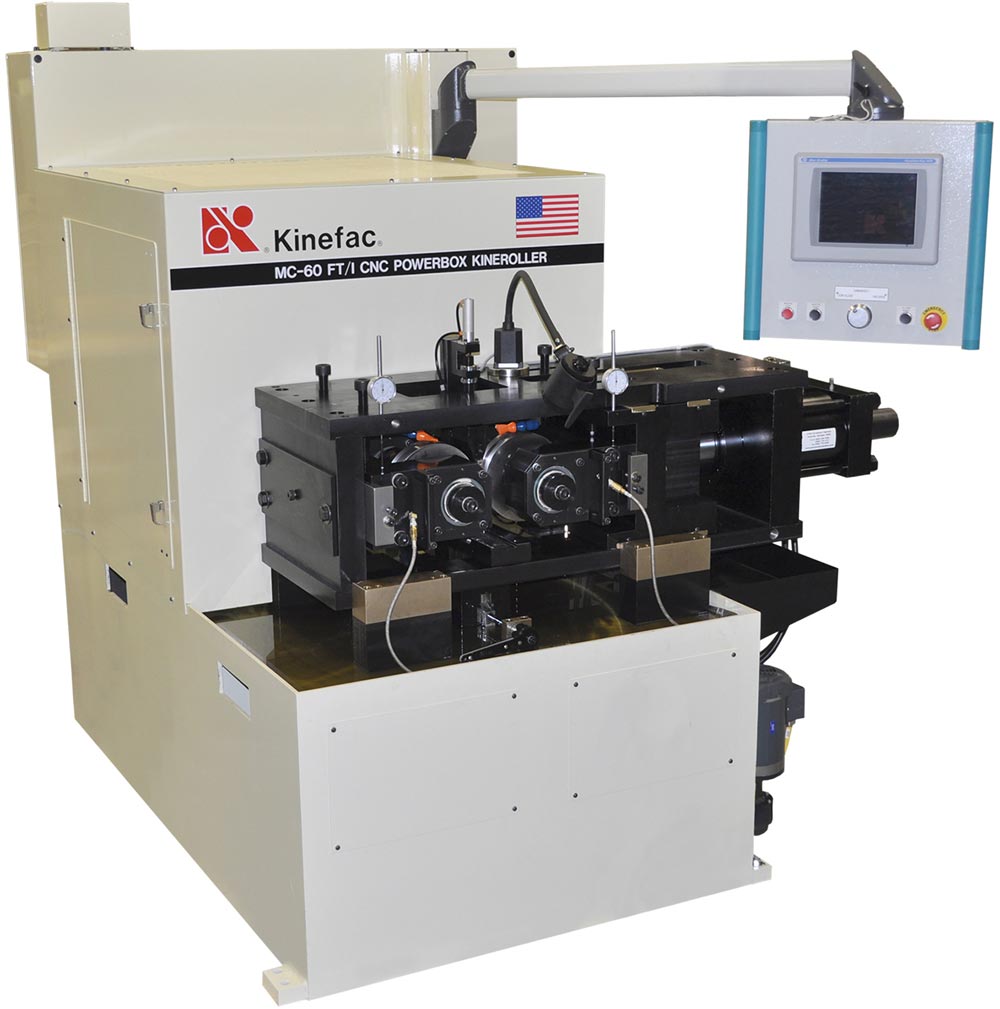
Ball Screw Rolling Process Control Features
True Die Position system
Chilled die and part lubrication systems
KINEFORM cylindrical rolling dies
Servo blade automatic height control systems
KineGlide low friction rolling blades
Flat blade, roller blade, bushing, and center support tooling
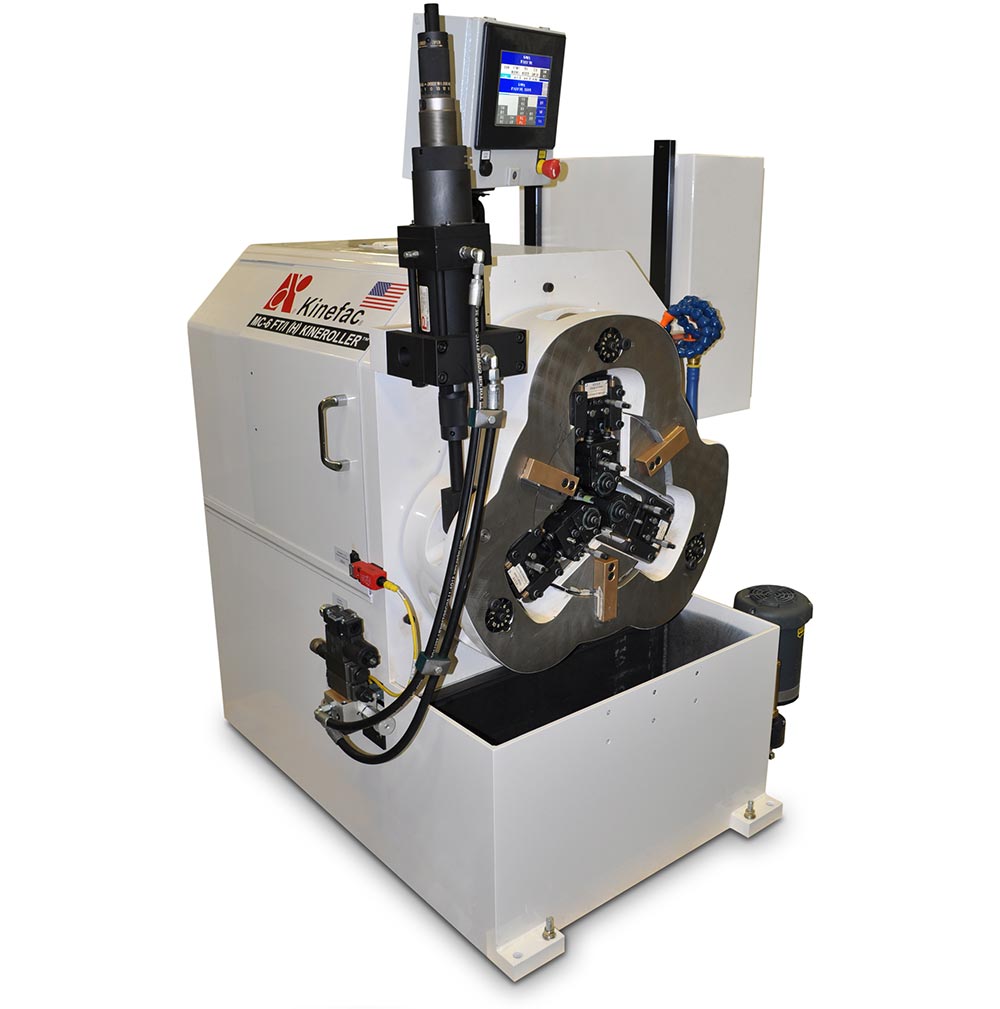