Cylindrical Die Rolling Process
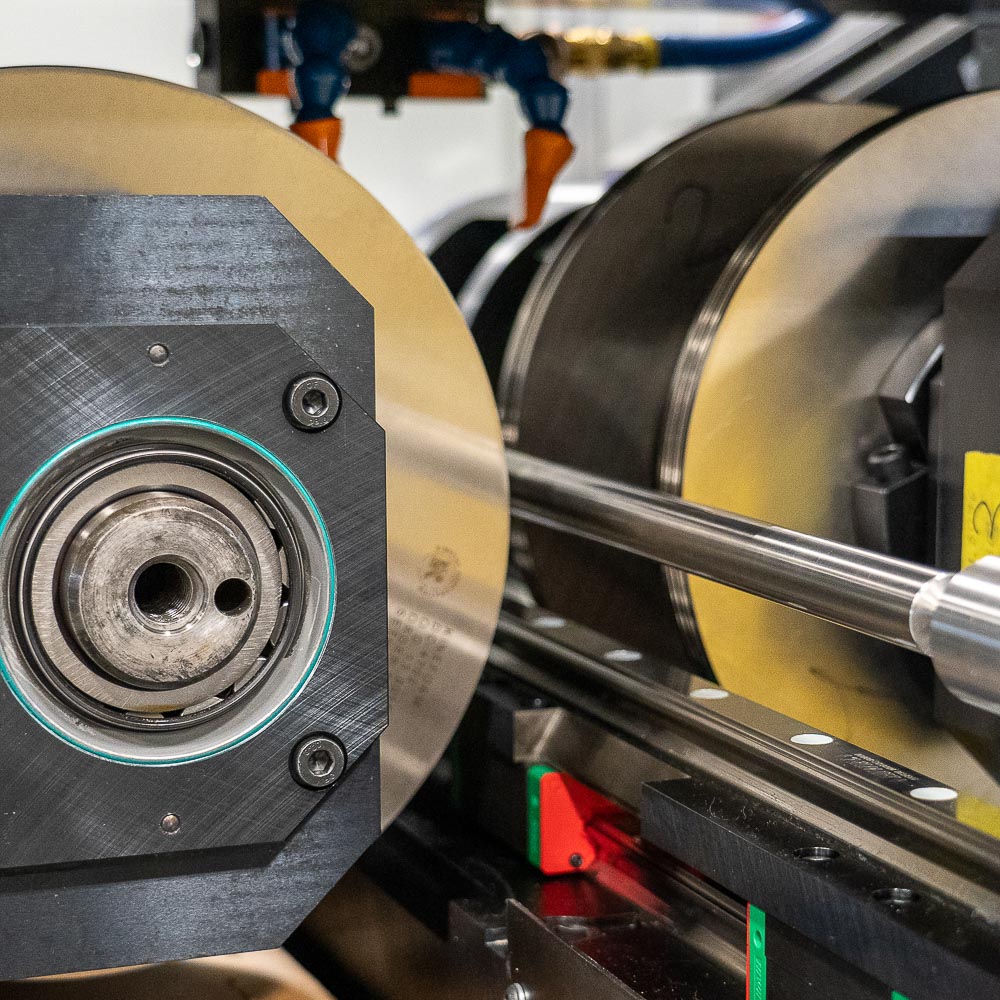
Cylindrical Die Rolling
Cylindrical die rolling is a metal forming process used to form screw threads and other helical, axial, and annular geometries on products such as fasteners, power transmission shafts, and precision lead screws. The rolled profile geometry is formed into the surface of a round blank by two or three round forming dies which have the inverse of the rolled profile on their surface. The dies rotate in phased relationship while they simultaneously penetrate the surface of the blank and force it to rotate by friction. The blank material is displaced radially into the precise shape of the dies by plastic deformation.
Material is not added or removed during the rolling process which can take just a few seconds to complete. Compared to traditional cutting processes, rolling can result in 20% material savings and can be more than 10X faster. The speed of roll-forming is generally governed by the ability to transfer energy through the dies and into the blank to deform the material.
Cylindrical die rolling is commonly applied to parts having pre-roll hardness up to the mid-30’s Rockwell C but can also be applied to parts with pre-roll hardness up to and exceeding Rockwell C 48. However, die life becomes very poor in this high hardness range. Rolling is typically carried out as a cold forming process with blanks at room temperature, but high hardness blanks can be rolled at elevated temperatures as a warm-forming process to help improve the metal flow.
Cylindrical die rolling is used to produce a variety of precision forms such as threads, worms, gears, splines, knurls, fins, and modified thread forms like ball screws and lead screws. It is well suited for processing precision parts with tight dimensional tolerances and statistical process control requirements.
Benefits of Cylindrical Die Rolling
|
|
Infeed Rolling
Infeed Rolling, also known as plunge rolling, is used to produce discrete lengths of rolled geometry by plunging the dies into the blank at controlled speed and then retracting them when the form is fully rolled. The dies and part are aligned on parallel axes to each other which results in little to no axial feed of the workpiece during rolling. When the dies have reached full penetration depth, they are held in fixed dwell position long enough to calibrate the roundness and fullness of the rolled form before being retracted.
The working face of the dies must be as long or slightly longer than the length of thread or form being rolled. The face width will also depend on the shape and configuration of the blank. Infeed rolling minimizes incomplete or under filled rolled geometry which typically occurs at the extreme ends of the rolled form. The area of under fill will be governed by the die edge chamfers or the blank chamfers. Infeed rolling allows threads and forms to be rolled very close to protruding features such as shoulders or heads with minimal cycle time.
Two-Die Infeed Rolling
Three-Die Infeed Rolling
Throughfeed Rolling
Throughfeed Rolling, also known as skewed axis rolling, is used to produce continuous lengths of rolled geometry by allowing parts to feed through the dies completely or for a controlled distance. The dies are on skewed axes with respect to the part which results in axial feeding during rolling. A throughfeed die has a starting section, dwell section, and relief section to accomplish controlled radial penetration of the blank, calibration of roundness and fullness the form, and disengagement of the die from the workpiece. The die face width is governed by the machine capacity and rolled form characteristics and is normally very narrow compared to the full length of rolled form.
A combination of infeed and throughfeed can be used to roll partial or full lengths on a part. This can result in incomplete or underfilled threads as the dies reach their rolling position while feeding takes place. The length of the underfilled thread section is dependent on the part feed rate, die geometry, and the plunge speed of the dies.
There are four main Throughfeed rolling modes:
- Straight Throughfeed
- Throughfeed & Open
- Infeed/Throughfeed
- Infeed/Throughfeed & Open
Straight Throughfeed rolling requires the dies to be positioned at fixed radial center distance. Blanks are introduced between the dies and are pulled through by the feeding action until the rolled workpiece leaves the dies completely. This type of rolling is used to produce full length rolled forms.
Throughfeed & Open rolling requires the dies to be at fixed radial center distance while the blank is introduced between them. The blank is pulled through by the feeding action until the dies are opened off the workpiece when desired length of rolled form is achieved. This type of rolling is used to produce partial length or full length rolled forms and can result in incomplete threads where the dies are opened.
Infeed/Throughfeed, also known as plungefeed, requires the dies to close onto the workpiece like the infeed process. Throughfeed action begins simultaneously as the dies penetrate the blank to their rolling position. Rolling is then carried out until part feeds through the dies completely. This type of rolling is used to produce full length or partial length rolled forms and can result in incomplete threads where the dies are initially closed.
Infeed/Throughfeed & Open requires the dies to close onto the workpiece and throughfeed roll until the dies are opened off the part when desired length of rolled form is achieved. This type of rolling is used to produce full length or partial length rolled forms and can result in incomplete threads where the dies are initially closed and where the dies opened.
Throughfeed rolling is primarily used for threaded rod applications and precision actuator screws for linear motion such as ball screws and lead screws.
Two-Die Throughfeed Rolling
Three-Die Througheed Rolling
Single Revolution Rolling
Single Revolution rolling, also known as incremental rolling, is used to roll discrete lengths of rolled geometry using one revolution of the dies to compete the rolling process. The dies are at fixed radial center distance and are aligned on parallel axis with the part which results in little to no axial feed of the workpiece during rolling. The rolled profile height gradually increases around the periphery of the dies in a starting section, maintains full height over a fixed circumference in a dwell section, then diminishes in height for a relief section. The penetration, dwell, and disengagement of the dies with the workpiece are all accomplished by the die design.
A single revolution die can also be manufactured with just a starting and dwell section without a relief section. The machine center distance control is used to open the dies and simulate the relief section. This can have the added benefit of extending die life by incrementally opening the dies further into the dwell section as normal tool wear progresses.
Single revolution dies typically have a cutout relief between the beginning of the penetration section and the end of the dwell section. This allows for part positioning and easy transfer through the dies.
This process can also be utilized to roll several independent forms on a single shaft by mounting multiple sets of single revolution dies on the same machine spindle. Shaft handling and over-all processing time is reduced. An alternator shaft with a thread and two serrations can be produced very quickly in a single handling by one machine rather than by three separate machines with handling between each.
Single revolution rolling is typically used to roll splines, serrations, knurls, threads, and worms, on power transmission shaft applications such as half-shafts and axle bars.
Single Revolution Rolling
Superior Cylindrical Die Rolling for Demanding Applications
Small Parts
Automotive Shafts
Medical Devices
Power Tool Shafts
Electric Motor Shafts
Bolts
Aerospace Fasteners
Precision Ball Screws
Ammunition Components
Construction Bolts
Hand Tools
Electric Connectors
Actuator Screws
Fittings
Threaded Rod
Large Parts
Aerospace Components
Nuclear Studs & Tie Rods
Turbine Disc Bolts
Ball Screws
Truck Components
Oil Field Components
Mine Roof Bolts
Compressor Shafts
Turbine Case Studs
Actuator Screws
Ordnance Components
Marine Hardware
Tower Constraint Rods
Construction Components
KINEROLLER Rolling Machines
High speed and high-quality form rolling
Sawed, sheared, extruded, forged, or headed blanks
On-demand automated system operation available
Which KineRoller is best for your application? Contact us.
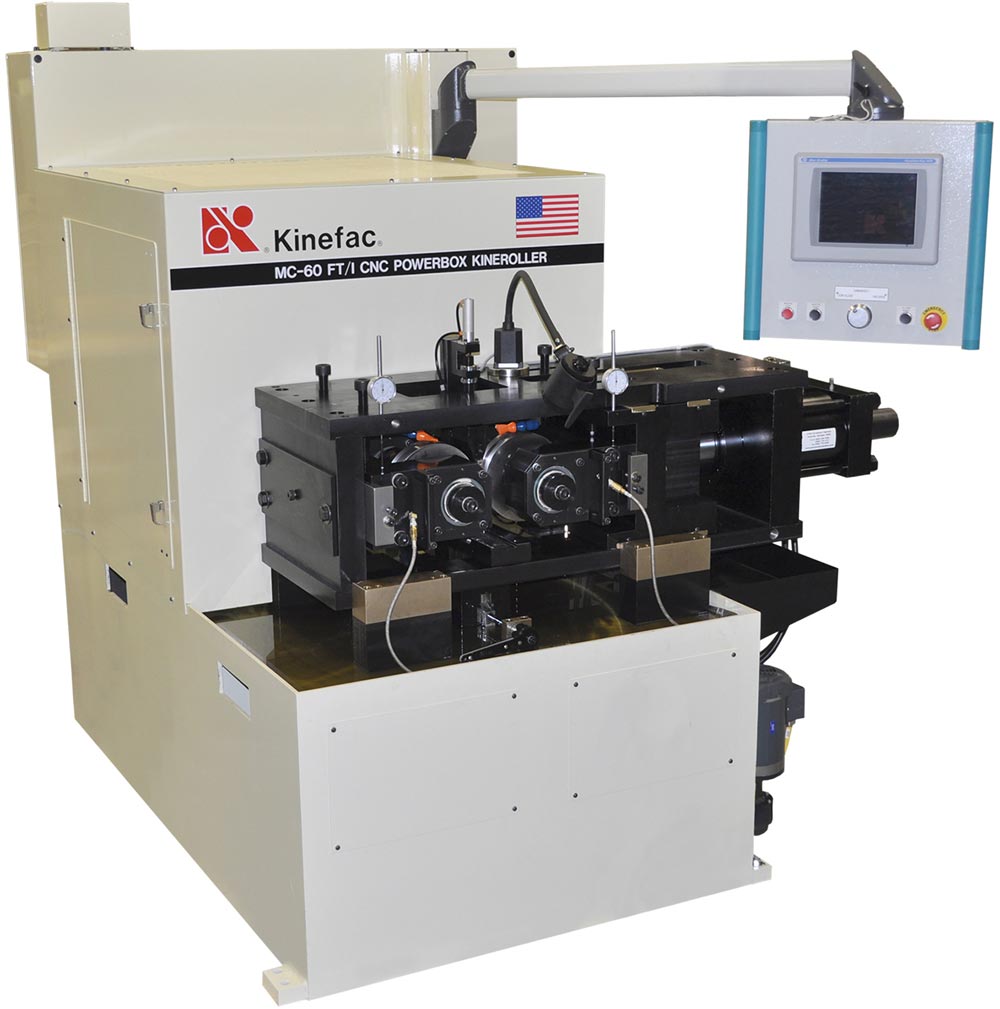
KINEROLLER Rolling Machines
High speed and high-quality form rolling
Sawed, sheared, extruded, forged, or headed blanks
On-demand automated system operation available
Which KineRoller is best for your application? Contact us.
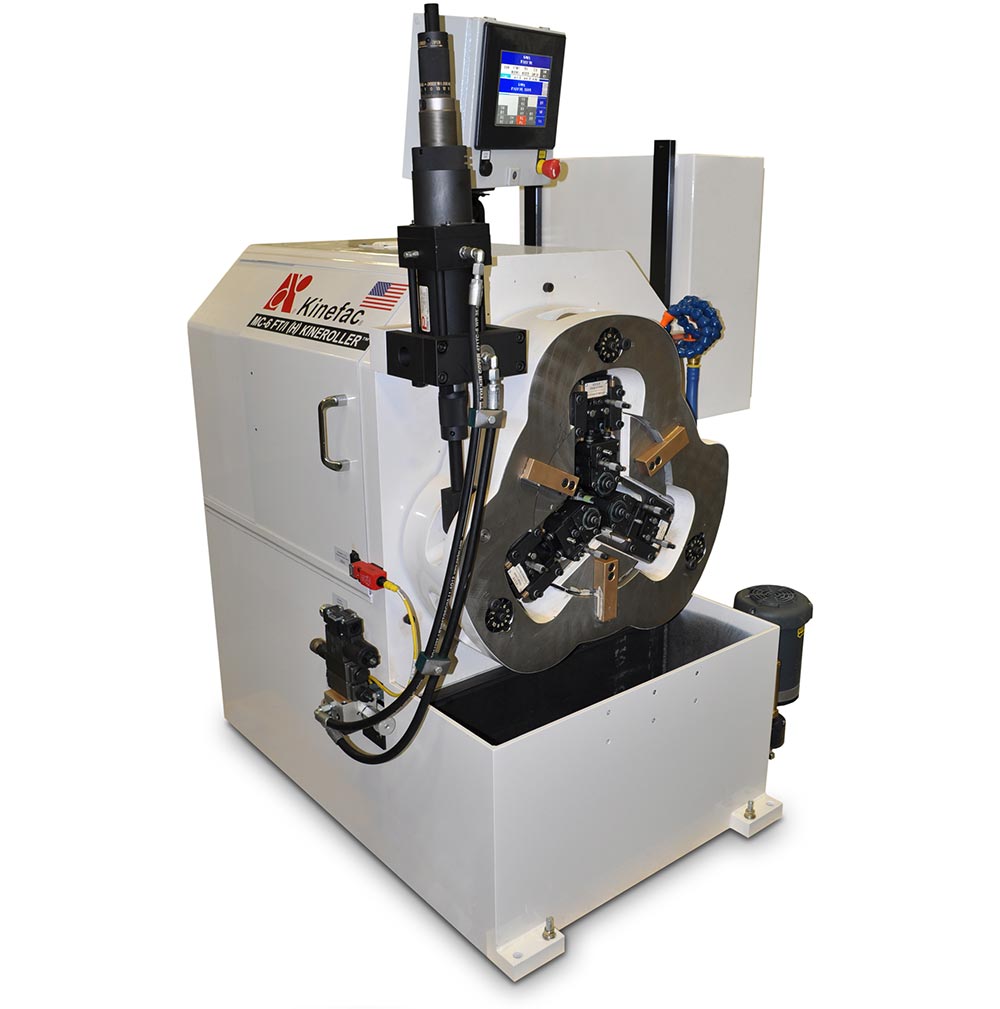